BSBWHS501 Ensure a safe workplace
Assessment Requirements
Performance Evidence
Evidence of the ability to:
Establish, implement, maintain and evaluate a work health and safety (WHS) management system for a work area of an organisation in accordance with WHS legislation including policies, procedures and record keeping
Ensure organisational WHS compliance
Establish, implement, maintain and evaluate effective and compliant participation arrangements for managing WHS including identifying duty holders, identifying and approving the required resources and developing and implementing a training program
Establish, implement, maintain and evaluate procedures for effectively identifying hazards, and assessing and controlling risks using the hierarchy of risk control
Provide information and complete documentation for a WHS management system
Identify requirements for and request expert WHS advice.
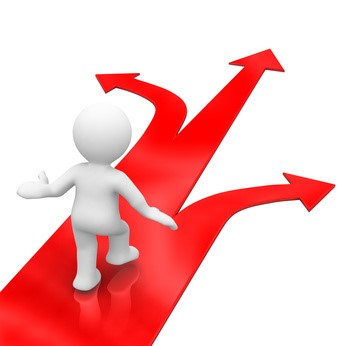
Knowledge Evidence
To complete the unit requirements safely and effectively, the individual must:
Identify and detail relevant WHS Acts, regulations and codes of practice
Specify relevant WHS organisational policies, procedures, programs and practices
Explain hazard identification and risk-management processes
Describe the hierarchy of risk control and how it is applied in the workplace
Specify in-house and WHS legislative reporting requirements.
Assessment Conditions
Assessment must be conducted in a safe environment where evidence gathered demonstrates consistent performance of typical activities experienced by individuals carrying out work health and safety duties in the workplace and include access to:
Organisational WHS policies and procedures
WHS legislation, regulations and codes of practice
Case studies and, where possible, real situations
Interaction with others
Assessors must satisfy NVR/AQTF assessor requirements.
Links
Companion volumes available from the IBSA website
Housekeeping Items
Your trainer will inform you of the following:
Where the toilets and fire exits are located, what the emergency procedures are and where the breakout and refreshment areas are.
Any rules, for example asking that all mobile phones are set to silent and of any security issues they need to be aware of.
What times the breaks will be held and what the smoking policy is.
That this is an interactive course and you should ask questions.
That to get the most out of this workshop, we must all work together, listen to each other, explore new ideas, and make mistakes. After all, that’s how we learn.
Ground rules for participation:
- Smile
- Support and encourage other participants
- When someone is contributing everyone else is quiet
- Be patient with others who may not be grasping the ideas
- Be on time
- Focus discussion on the topic
- Speak to the trainer if you have any concerns
Objectives
Discover how to establish a WHS management system in a work area
Know how to establish and maintain effective and compliant participation arrangements for managing WHS in a work area
Learn how to establish and maintain procedures for effectively identifying hazards, and assessing and controlling risks in a work area
Understand how to evaluate and maintain a work area WHS management system
Gain skills and knowledge required for this unit
1. Establish a WHS management system in a work area
1.1. Locate, adapt, adopt and communicate WHS policies that clearly define the organisation’s
commitment to complying with WHS legislation
1.2. Identify duty holders and define WHS responsibilities for all workplace personnel in the work area according to WHS legislation, policies, procedures and programs
1.3. Identify and approve financial and human resources required by the WHS management system (WHSMS)
1.1 – Locate, adapt, adopt and communicate WHS policies that clearly define the organisation’s commitment to complying with WHS legislation
Clearly defining commitments to WHS legislation
All organisations must have an effective system to manage Work Health and Safety (WHS). As a manager your primary goal should be to develop a dynamic system that is responsive to minimising hazards that can cause injury, disease and death in the workplace. It is imperative that the system is committed to the development of policies and procedures working within Australia's legal system.
Currently, WHS law within Australia comprises of state territory and Commonwealth legislation. For legislation within your state or territory please refer to the regulators found in the reference section.
The Government of Australia and her states and territories are currently working at harmonising the WHS legislation and regulations in Australia. However, this is a goal and current separate state/territory and Commonwealth law still apply.
WHS legislation found within this guide shall relate to the Model Work Health and Safety Act 2011, introduced 1 January, 2012.
To ensure that an effective WHS system is developed, it is important that policies and procedures are developed.
These may be based on:
- Control of risks
- Contractor’s and employee's duty of care
- Employer's duty of care
- Health and safety committees and representatives
- Inspections
- Manual lifting
- Risk assessments
- The recording and/or documenting of WHS information
- Training
- Workplace discrimination.
Policies and procedures need to be readily available and accessible to all staff in regards to policy and procedures. Locating WHS policy and procedures will depend on where you work and the type of business operating.
WHS policies and procedures
Paper based format
A hard copy is usually found in most organisations’ main office. If you work in a factory environment, hard copies will usually be found strategically throughout the production area. Paper based copies are usually intended for when staff members are unable to access the internet. However, some organisations do prefer to ensure that hard copies are available to all staff.
Electronic format
Electronic copies of WHS policy and procedures can usually be found on an organisations intranet. An intranet is an interconnected network of computers found in an organisation protected from outside exposure. This information is usually internal to the organisations operations.
The legislative framework that your organisation operates usually stems from the requirements of:
The Act
An act aims at ensuring that WHS is managed effectively in the workplace by ensuring that employees are protected under their Commonwealth, state and territory laws.
Harmonised work health and safety law which aims to ensure work health and safety laws provide regulators with functions.
These laws provide:
Advice and information to duty holders and the community
Monitoring and enforcing compliance with work health and safety laws
Fostering co-operative, consultative relationships between duty holders and the persons and representatives they owe a duty to
Sharing information with other regulators
Conducting and defending proceedings under work health and safety laws.
Until recently, the Commonwealth, state and territory governments were responsible for making and enforcing their own health and safety laws. Even though, these jurisdictions are similar, the variations led to confusion. By developing the WHS laws, Safe Work Australia, working with the Commonwealth, state and territories harmonised the act, regulations and codes of practice.
Some states and territories chose to delay the implementation of this WHS legislation. Please refer to your regulator to determine when this legislation will be implemented. Please note that in most instances, the regulators actively encourage workers to follow the new legislation.
Regulations
The Work Health and Safety Regulations 2011, provide you with a lot of structure within a statutory framework that has been created by Statute to give you details on how to implement legislation. Unless you can provide a better alternative, regulations are mandatory.
These regulations cover:
The Health and Safety Representative election processing
Statutory notices
The details about incident notifications
Changing definitions of “Worker”
Rights and responsibilities of WHS representatives and committees
Right of entry for WHS inspectors
Problem resolution procedures.
Codes of practice
Unlike with regulations, whereby you can be charged for not following them, codes of practice are written to provide guidance on how to maintain a safe workplace. However, by demonstrating that you are following a code of practice, you can provide sufficient evidence to demonstrate that you are following the law. The code of practice is based on the WHS Act 2011.
These codes of practice include:
How to manage work health and safety risks
Managing hazardous manual tasks
Managing the risk of falls at workplaces
Labelling of workplace hazardous chemicals
Preparation of SDS for hazardous chemicals
Dealing with confined spaces
Managing noise and preventing hearing loss at work
WHS consultation, cooperation and coordination
How to safely remove asbestos
How to manage and control asbestos in the workplace
First-aid in the workplace
Managing construction, demolition, and excavation work
Preventing falls in housing construction
Managing risks of plant in the workplace
Managing risks of hazardous chemicals in the workplace
Safe design of structures
Managing electrical risks in the workplace
Welding processes
Spray painting and powder coating
Abrasive blasting
Preventing and managing fatigue in the workplace
Responding to workplace bullying.
In April 2014 the Select Council on Workplace Relations agreed to ask Safe Work Australia to review 12 draft model codes of practice. This was to ensure they were clear, concise and practical and that they took all sectors of business into account including small business, without compromising safety standards or imposing any further regulatory burden.
The review has been completed. Nine of the draft model codes have been agreed by the majority of Safe Work Australia members as national guidance material.
Safe Work Australia has published nine packages of material for:
Workplace traffic management
Managing cash-in-transit security risks
Managing risks in forestry operations
Industrial lift trucks
Amusement devices
Safe design, manufacture, import and supply of plant
Working in the vicinity of overhead and underground electric lines
Formwork and falsework
Scaffolds and scaffolding work.
Standards Australia
A standard is a document that provides you with a safe, reliable and consistent work environment. They assist you in defining quality and safety criteria to assist in working towards a safe workplace.
The WHS Consultation, Cooperation and Coordination Code of Practice 2011, requires that the consultation process be a two way process. Management must actively seek worker views and address worker concerns in relation to health and safety hazards in the workplace. For workers to make informed recommendations, management must ensure that workers are provided with relevant information.
Information must be easily accessible and in a manner that workers can understand. This means that as a worker, you should make sure that you know where to find organisational policies and procedures in your work area.
Information must also be communicated to workers. Information is communicated by management as per the agreed format as part of the communication process. As such, if workers and/or their representatives agreed to work group meetings or emails as the agreed communication process then management must ensure that information is communicated in the appropriate format.
Activity 1A
1.2 – Identify duty holders and define WHS responsibilities for all workplace personnel in the work area according to WHS legislation, policies, procedures and programs
WHS responsibilities for all workplace personnel
The Work Health and Safety Act 2011, is now administered by the regulators for your state or territory.
Section 28 of the WHS states that while at work, a worker must:
1. Take reasonable care of his or her own health and safety
2. Take reasonable care that his or her acts or omissions do not adversely affect the health and safety of other persons; and
3. Comply, so far as the worker is reasonably able, with any reasonable instruction that is given by the person conducting the business or undertaking (PCBU) to allow that person to comply to the act
4. Cooperate with any reasonable policy or procedure of the PCBU relating to the health or safety at the workplace that has been notified to the worker.
As a worker, you will usually be provided with job descriptions that will set out your roles and responsibilities under the WHS Act. Management should notify you about changes to the roles and responsibilities and you have a legal obligation to follow their policies and procedures.
If you feel that you are at risk, you have the right to say no. However, make sure that you give the reason why you are unable or unwilling to perform a task.
Section 19 of the WHS Act, 2011, sets out the employer’s primary duty of care. This duty of care requires that, as far as reasonably practicable, the person conducting a business or undertaking must ensure that the health and safety of workers and other persons is not put at risk from work carried out as part of conduct of the business or undertaking.
Policies and procedures are developed to ensure that a systematic approach to WHS is maintained to ensure that risk is minimised in the work place.
‘Hazard’ means a situation or thing that has a potential to harm a person.
Hazards may include:
- Noisy machinery
- A moving forklift
- Electricity
- Repetitive work.
‘Risks’ are the possibility of harm, death, injury or illness that might occur when exposed to a hazard.
Risk management is important to ensuring that risk is minimised in the workplace. As a manager, it is important that you know and understand your responsibilities under law.
Effective risk management starts with a commitment to health and safety from those who operate and manage a business. Workers must be involved and cooperate with health and safety. For this to happen, workers need to see that managers are committed to WHS.
Commitment is achieved when management:
Demonstrate commitment to workers by sharing information in the consultation process
Provide resources such as training to ensure that tasks are completed safely
Ensure that workers and other stakeholders understand their responsibilities under the WHS act and regulations and associated codes of practice.
By developing policies and procedures you are ensuring that you are not only following your legislative requirements, you are also managing risks to safety which is one of the employer’s general duties of care.
Risk management is important to ensuring that risk is minimised in the workplace. As a manager, it is important that you know and understand your responsibilities under law.
When seeking advice from experts or general advice, you may contact your state/territory body or Comcare who can provide you with advice or recommend another body that can provide you with advice.
For any WHS system to thrive it is the responsibility of senior management to lead by example. Merely stating that you support the WHS framework in place within the organisation is not sufficient in ensuring that all members of staff support the WHS system.
Management must demonstrate their commitment to WHS because responsibility starts at the top. This commitment must be demonstrated by ensuring that a safe culture is demonstrated by supporting employees and taking the time to provide the training that they require. If management does not reflect their words in support, then staff will be disappointed and it will make it harder to inspire them to follow WHS procedures and participate in WHS.
The WHS Consultation, Cooperation and Coordination Code of Practice 2011, provides management with the foundation upon which support for WHS can be obtained and retained.
Section 47 of the WHS Act requires that you consult, so far as reasonably practicable, with workers who carry out work for you, who are, or are likely to be, directly affected by health and safety matters.
Section 48 requires that, if the workers are represented by a health and safety representative, the consultation must involve that representative.
Consultation involves the process of:
Sharing information where management provides workers information that will assist them in providing feedback.
Giving workers the chance to express their views and address their concerns to management
Management should then provide workers with time to provide this feedback, which they use to make objective decisions under the WHS Act. Note that management does not have to make a final decision based on this feedback, but must consider the feedback as part of the decision making process.
Providing workers with feedback on their decisions in a timely manner.
The consultation process includes the development of an agreed communication process that allows management to communicate new roles, responsibilities and systems to workers. When a worker elects a health and safety representative (HSR), this means that management should direct their communication and the consultation process to the HSR.
Management should:
Implement safe work systems
Actively encourage the reporting of incidents
Look for opportunities to improve
Value staff contributions by acknowledging and involving them in the decision making process
Provide safe and effective support to complete their roles safely.
Management commitment is necessary but not compulsory to ensuring staff are committed to WHS.
When management show commitment and consistency, the results are:
Greater loyalty
Changes in systems.
The role of senior management
The writers of the organisations vision and mission need to have the foresight to know where the organisation is heading. In correlation to this direction, they are also required to ensure that the quality of their product is maintained and continuously improved to demonstrate that they care for their client. As such, senior management should identify the steps to ensure that the organisations vision is realised.
This can be achieved by:
Ensuring that WHS performance levels are competitive
Making sure all staff have a clear idea of their roles and responsibilities
Promoting a culture of continuous improvement
Creating an environment built on trust, active participation and cooperation
Ensuring that a structure is in place for a consultative process
Ensuring that information is shared by all
Ensuring that risk management processes are in place that protect all within the organisation
Developing a WHS management information system.
Each of these should be the driving force of an organisation’s WHS policies and procedures. Performance monitoring and evaluation tools should be designed to ensure that the organisation is meeting all of its goals and outcomes safely.
Senior management set the strategic goals which pave the way for middle management to develop tactical goals that are then put into operation by work groups. For example, management's strategic goal may be to decrease the incidence of incidents/accidents by five per cent in 2011. One tactical way in which to create awareness and reinforce learnt skills is by identifying gaps in employee knowledge, and then taking steps through training and development to improve workers skills and knowledge levels.
In turn, as the gap between the employee’s current knowledge and their future desired knowledge is filled, then theoretically this knowledge should decrease the level of incidents or accidents in the workplace.
All staff involved in work activities should know the expected outcomes of the job and each and every safety responsibility that they have. These roles and responsibilities should be reflected in their job descriptions.
A job description is a list of the general tasks or functions and responsibilities of the jobs position. Job descriptions need to clearly and concisely communicate employee responsibilities, the tasks of the job and to indicate the basic requirements for the job.
Job descriptions
A well-written job description includes:
Title of the position
Department
To whom the person directly reports
Overall responsibility
Key areas of responsibility
Those who the person works with on a regular basis
Terms of employment
Qualifications.
From the job description you will be able to determine the policy and procedures that will apply for the position. These procedures will assist employers in controlling the level of safety required to be demonstrated in the workplace. Such requirements are either performance based or process based.
Performance based standards
Performance based standards aim to provide you with the compliance standards you need to demonstrate through goals and outcomes. They also show you how to solve a problem or how to escalate it to another member of staff to work out.
Process based standards
Process requirements prescribe a series of steps that must be followed with the aim of managing specific hazards, or WHS generally. They are often used when the regulator has difficulty specifying a goal or outcome, but has confidence that the risk of illness or injury will be significantly reduced if the specified process is followed. Most regulations now require the duty holder to identify hazards and assess and control identified risks.
Process-based standards have spawned greater reliance on documentation requirements. Increasingly WHS regulations are requiring duty holders to document measures they have taken to comply with process-based standards, performance standards and general duty standards.
As the focal point of WHS, it is important to know the role of a safety officer.
These roles include:
Providing WHS advise
Assisting in risk management
Liaising with WHS representatives
Consulting with Health and Safety Representatives (HSR) about safety issues
Assisting in the promotion of WHS
Auditing and analysing WHS issues.
In Queensland, the role of the Workplace health and safety committees is to:
Encourage personnel to maintain an interest in WHS in the workplace
Identify gaps in skills and arrange for training and development in WHS issues
Keep up to date with changes in legislation
Review and investigate workplace health and safety
Provide advice to employers on how to address safety issues.
The health and safety representative needs to be a part of this committee as a representative for the co-workers who elect them, to represent them in workplace health and safety issues. It is also important to note that in Queensland, any employer who employs 30 or more workers normally must appoint a workplace health and safety officer.
Activity 1B`
1.3 – Identify and approve financial and human resources required by the WHS management system (WHSMS)
Financial and human resources
No health and safety systems will operate without the resources to meet the goals. For example, training can be time consuming and expensive. If your organisation does not have the funds available to ensure that training takes place, then injuries will occur. In this case another viable alternative should be considered. Mentors and coaches with the required skills, knowledge and experience working already within the organisation will ensure that the expected outcomes are reached and maintained.
When determining the resource needs of the organisation, it is important to ensure that you not only operate within the budget, you should also ensure that you understand the resources available to you.
Human resources can include the costs of:
Contracting personnel as opposed to hiring a full time employee to maintain WHS
Investigating incidents
Non-compliance and the resultant impact they would have on the organisation
Required risk and WHS personnel.
Financial resources can include:
Allocated budget, whether one budget for all or a separate budget for each department.
Cleaning
Updating facilities and equipment
Providing materials to minimise risk
Training.
After identifying all of the costs, it is important that you reflect on what outcomes you are trying to achieve. Are the resources sufficient to meet WHS goals and outcomes? If they are not, what alternatives are available? Management will not automatically approve a resource because it is the only one you recommend.
Of course, there are costs that cannot be avoided, but they can be minimised without placing anyone at risk. We shall look at these in more detail later in this manual. For now, let us consider this example.
For a manager to obtain approval for a resource, you need to demonstrate:
That you have researched the problem
o records are one way in which to research the problem. Risk assessments, injury records, training, workers compensation records, costs of equipment, fire and security records and their associated costs may even assist you in answering the problem.
§ however, there may be times when you will need to consult with others for information. How much time and effort allocated to your research will vary according to the level of perceived risk. If you are to find an answer to your problem, you need to make sure that you can demonstrate that you have researched the problem.
That you have reviewed all of the data
o even if you do not use all of the data available to you, demonstrate that you have at least looked at it and reviewed it as long as it is relevant to the problem
That you have considered the risk involved
o when applying for approval, demonstrate that you have considered all options.
That you make recommendations based on your findings
o reinforce all arguments and recommendations with facts. Most organisations are outcome based, so make sure that all of your recommendations are outcome based.
This is just an example of the steps you may require to obtain approval for the effective operations of the WHS system in your workplace.
Activit y 1C
2. Establish and maintain effective and compliant participation arrangements for managing WHS in a work area
2.1. Work with workers and their representatives to set up and maintain participation arrangements according to relevant WHS legislation
2.2. Appropriately resolve issues raised through participation and consultation arrangements according to relevant WHS legislation
2.3. Promptly provide information about the outcomes of participation and consultation to workers and ensure it is easy for them to access and understand
2.1 – Work with workers and their representatives to set up and maintain participation arrangements according to relevant WHS legislation
WHS management systems
The goal of most WHS management systems is to ensure that the workplace is free of risk, injury and disease. To ensure a system of information sharing both the employer and employees must work together to meet this goal.
For an effective and efficient WHS management system to thrive there needs to be a mutual bond of respect between management and their team members.
This means that:
Team members must participate in WHS issues
Management must consult with employees on WHS issues.
Under Section 16 of the Commonwealth WHS Act (1991), an employer must take care to protect the health and safety of employees, including under subsection (d), making sure to develop written health and safety management arrangements.
These arrangements will:
Enable effective cooperation between the employer and employees in promoting and developing measures to ensure the employee's health, safety and welfare at work
Provide systems to inform employees, review variations and their effectiveness, provide resolution to disputes and establish a WHS committee if required.
Conversely, employees have a duty under section 21 to:
Not put anyone at risk
Follow the employer's instructions
Use equipment in the correct way.
In short, this means that employers must consult with employees in regards to WHS issues, while employees must legally provide information all in the effort of ensuring the workplace is safe. For example, participation includes employees reporting unsafe practices and encourages team members to report unsafe practices, to take steps to identify, assess and control unsafe practice, broken equipment and participating in opportunities to be consulted.
Information between management and team members should flow smoothly. The method in which the information flows shall be influenced by the type of industry and the type of employees that are employed in the organisation. For example, if you work in an industry with a low skill level, then meetings would be the preferred manner in which information would be shared with staff. Graphs and tables would then be used to convey factual information.
Conversely in a professional setting, information would be shared via email or reports, depending on the staff members’ position in the organisation.
In the same way, information may be conveyed differently between employee and their employer. For example, some team members may prefer meetings as a form of open forum where ideas can be put forward. However, some personnel with low self-esteem may not be confident enough to speak up. To obtain the full advantage offered by a consultative process, it is important that you encourage all of your team members to participate in the process.
Informal consultation
Informal consultation involves meetings, telephone calls, discussions and letters. When you consult with staff that are difficult to reach or shy, you will be in a better position to meet your duty of care under the WHS Act.
Formal consultation
Formal consultation arises when specific information is required. For example, you may design a questionnaire or staff feedback form to identify if there are any issues that you believe may be important and may be blocking the continuous improvement process. By asking specific questions, you can clarify issues and identify possible causes and resolutions.
Findings of course will vary according to the questions set out in either the questionnaire, interviews or feedback forms.
2.2 – Appropriately resolve issues raised through participation and consultation arrangements according to relevant WHS legislation
Consultation
Consultation is not only an organisation’s legal responsibility; it is also an important part of the planning process.
Benefits of consultation are:
Provides a means in which to resolve WHS issues derived from team members experience and knowledge
Builds a greater sense of commitment as workers take ownership for their actions
Strengthens relationships and morale as people's sense of self-worth increases
Can provide an increase in productivity as staff takes WHS on board.
Consultation is needed to:
Improve on processes
Assist in the decision making and resolution process
Assist in consultative procedures.
A WHS framework can be designed to establish a culture in which consultation and cooperation exist. This means that when your management designs a health and safety management arrangement (HSMA), you the employee must be consulted.
Participative arrangements are a major characteristic of an effective occupational health and safety (WHS) system. There needs to be a clear channel of communication between all stakeholders in WHS. Participative arrangements and consultation are the link between these parties to ensure that a unified approach to a healthy workplace is devised.
Information sharing and consultation provide a balance so that individuals form a whole in which they become unified in WHS. It is your role as a manager to ensure that information is accessible to staff and that management consults with their team. Take the time to acknowledge the employees participation in WHS and provide them with feedback and they will become empowered.
Empowerment aims to give individuals power over aspects of their lives. By sharing information and consulting with them, you are empowering them and building their confidence. This type of participation ensures that your team will take ownership of their positions and follow their duty of care by identifying hazards and minimising risk.
However, this does not necessarily mean that no problems will arise in the communication process.
Causes of conflict may include:
The failure of management to resolve an issue fast enough. This lack of responsiveness may result in an accident that may lead to an injury and in some instances death. If management could have overcome the problem and acted quickly enough, then the incident may not have occurred. This lack of action can lead to resentment and a loss of interest from team members.
Failure to react to the problem
Failure to take sufficient action to ensure that the workplace is safe
Failure to provide sufficient information so that staff members can’t make an informed decision.
The failure to take sufficient action or provide sufficient information will not only leave you open to litigation, but will also undermine your position and any respect you may have established sharing information or consulting with your staff will be lost. You must be consistent. Providing information that is accurate and consistent must be reinforced with actions that are responsive to ensure that your team stays empowered.
There is much research to prove that once management loses respect, it is very hard to get it back. To be a good manager, it is imperative that you practice what you preach.
Activit y 2A
2.3 – Promptly provide information about the outcomes of participation and consultation to workers and ensure it is easy for them to access and understand
Employer and employee information sharing
To provide a safe work environment, you must provide employees with information in a manner that is easily accessible to them. This means that the level of access that is given to employees is determined by the level of authority the employee has and the type of industry that you operate in.
Information that management may need to provide staff with will vary.
The strategic position and policy of the organisation
An organisation that has a mission and vision statement will usually clarify the current and future position of the organisation. Plans, statements and goals, policies and procedures are developed to reflect the organisation’s compliance and where employees stand in the organisation’s hierarchy. These definitions will assist you in determining what information is relevant to which staff and how you can communicate that information to your team.
The organisation’s risk management plan
Staff should only really be given the information that they require to make informed decisions. For example, you work in a production plant. One of your suppliers is constantly late with an order. To make sure that production does not stop, your fork lift drivers work faster to meet the organisation’s goals.
By working faster, they are meeting their work objectives but this is at the risk of the safety of the team. Who would you provide information to? What information would you provide? Would you provide all of your team with the information required to resolve the problem? Would the result of a risk assessment assist the purchasing officer in the ordering of stock? No. What they should be provided with is the fact that there is a problem, what the problem is and whether they can suggest any ways in which to encourage the supplier to ensure that their supplies arrive just in time.
Conversely, the fork lift driver needs to know that by speeding up to meet their objectives; they are placing staff and themselves at risk. The fork lift driver would need to know the impact of working too fast, as unrealistic goals leave whole new opportunities for mistakes to happen that put other lives at stake.
Risk analysis tools
No matter how much information you supply staff with the final decision will be yours. When you obtain feedback from your team, you need to have the ability to disseminate it in a logical manner so that you can provide the team member with your findings.
Risk analysis tools, such as the decision tree analysis, can assist you in determining the course of action you should take. By obtaining a clear picture of the risks and rewards associated with each possible course of action, you will be able to determine the best course of action to take.
Of course, you should make sure that you never lose sight of the fact that you need to acknowledge and give positive reinforcement to team members so that they will continue participating in the consultative process.
Access to internal and external specialist assistance
There are times in which you will be unable to assist your team members in specific WHS issues. You should provide your team with access to these specialists. For example, your team is employed to work on a production line. The introduction of a new part has caused a problem in the way in which the part is added to the whole production process. During the risk assessment, team members have made a suggestion about changing the work area to minimise risk. They may require the assistance of an engineer to ensure that their changes are realistic.
Conversely, you may need feedback from external sources to ensure that any changes that you recommend are within the confines of the law. Part of empowerment of your team is providing them with the resources to make recommendations that are valid, within the confines of the law.
Maintaining the risk register and giving appropriate staff access to historical data
Historical data is data that has been kept and maintained to ensure that your organisation has a history of the hazards that have been identified in the workplace, how the risks were controlled and/or resolved. The risk register can provide team members with a history of specific incidents that will assist in resolving other issues.
By knowing how a problem was rectified previously, you can either use the previous resolution to the problem or use the resolution to the problem as a stepping stone as part of the organisations continuous improvement process.
Hazard and associated risk register
Workplace area or grouping Ref No: __ Form completed by: _____(print)___(sign) Date form completed: / / | |||||||
Ref No. |
Hazard |
Associated risk |
Risk rating |
Control measure |
Control measure implemented? |
Review date | |
Yes |
No | ||||||
1264 |
Electrical shock from exposed computer wire |
Worker nearly died from electrocution |
H |
Turn electrical lead off. Tag the computer. Arrange for technician to repair. |
11-2011 |
Remember also that at the same time, you are also following your organisation’s legal obligation to follow WHS laws and maintain WHS records.
Providing training and support for staff
There will be times when WHS issues will arise that are outside the company’s level of experience. There may be other times in which the company may expand to such a level that a WHS representative or committee are elected in. To ensure that employees understand WHS, you may need to provide them with training to perform the functions required to meet their obligations as WHS representatives.
Training may also be necessary if new procedures are implemented that require more skill than previously required.
No matter what form of training and why training is taking place, it is important that employees are aware of the purpose of their training. Ask for feedback to ensure that their needs are being met. The feedback is important because it contributes to the consultative process and ensures that they participate in WHS.
When managing risk it is important to investigate the factors that can impact on the level and type of risk that occurs. There are many factors that will impact on the level of risk that applies to each individual risk in the workplace.
Common factors that can impact on risk may include factors relating to:
Commercial and legal relationships
Economic circumstances and scenarios
Human behaviour
Natural events
Potential circumstances
Technology – technological issues
Management activities and controls
Individual activities.
By identifying the cause of a risk and influences that impact on the severity of a risk, management will be able to identify ways in which to ensure that risks are minimised. Risk awareness will ensure that management will remain aware of what impacts on the work area and can identify ways in which to control and in turn minimise the risk.
However, it is essential that employees are aware of what their managers are trying to establish. Using pre dated information cannot in fact assist in resolving current issues. New innovations, budgetary constraints and lack of key staff with current information can in fact do more damage than good. The consequences could also see your organisation being fined for not maintaining your legal obligation to provide the employees with a safe work environment.
Information must be made available to all staff within their level of authority so that they can take the required steps to protect themselves. The more current the information is, the better the position of the team members will be. They will be able to provide you with informed ideas, suggestions and requests. This information should be accessible at all times. If a problem is identified, employees should be able to access possible resolutions before the problem evolves into putting team members at risk.
Level of authority
In several instances, you may have noted that we have touched on a staff member’s level of authority. Employees’ level of authority can be found in an employee’s job description and the policies and procedures pertaining to the employee. The information provides you with the level of responsibility that employees are able to make decisions at.
The level of authority that a staff member has should correlate with the level of information that they have. For example, a member of the production line should not be automatically provided with customer information. Contacting a client without clearance to do so can have a negative impact on the customer relationship with the company. An untrained member of staff may consult with the incorrect personnel and breach privacy laws.
As a part of their empowerment, employees should be able to have the confidence to contact you and/or another member of management and obtain access to consult with external parties. Using their initiative should not be stopped, but should be monitored to ensure that no breaches of the law arise.
It is essential to make sure that your client’s confidentiality is not breached, except when you have a legal obligation to divulge the information.
When providing information to staff, you should always:
Ensure that staff are aware of what the problem is
Be aware of how the problem may affect them
Advise them of suggestions made in managing the risk so other alternatives are considered; and
Assist in determining the feasibility of another suggestion.
Employees will give you different alternatives in providing different ways in which to control risk and keep the workplace safe.
When determining the feasibility of the suggestions that staff make, you should consider:
The cost or resources that are being recommended
The costs of training
The existing level of skill that your staff has; and
The difference between the current skill level and the future desired level of skills.
In short, the employees need to be provided with information in a format that is easily accessible and easy to understand. When making a decision, care should be taken to ensure that employees clearly understand what is required of them so that they can identify a potential risk and take the appropriate action to minimise the risk.
Some information is as easy as looking on notice boards or reading emails. However, the formatting of the information is also important. For example, providing percentages in a graph is clearer than writing a description of findings. The use of charts can be the basis around which a report is developed, where the graph could be used to explain basic changes to your team.
Activity 2 B
3. Establish and maintain procedures for effectively identifying hazards, and assessing and controlling risks in a work area
3.1 Develop procedures for ongoing hazard identification, and assessment and control of associated risks
3.2 Include hazard identification at the planning, design and evaluation stages of any change in the workplace to ensure that new hazards are not created by the proposed changes and existing hazards are controlled
3.3 Develop and maintain procedures for selecting and implementing risk controls according to the hierarchy of control and WHS legislative requirements
3.4 Identify inadequacies in existing risk controls according to the hierarchy of control and WHS legislative requirements, and promptly provide resources to enable implementation of new measures
3.5 Identify requirements for expert WHS advice, and request this advice as required
3.1 – Develop procedures for ongoing hazard identification, and assessment and control of associated risks
Identifying, assessing, and controlling risks
Hazard identification is the process by which a situation or event is identified that could bring injury or illness to others. Risks arise from hazards that have the potential to cause an accident, injury or illness to arise.
When considering associated risks in regards to a hazard; you need to reflect and consider:
The probability that the hazard will lead to an accident
The consequences if the accident happens; and
The stakeholders’ degree of exposure to risk.
When you are in the process of assessing the level and acceptability of risk associated with a given event, the quintessential question that you are required to ask yourself is “At what level does your organisation assess the level and acceptability of risk associated with a given event?”
To understand this level and acceptability of risk, it is important that you determine the type of risk analysis you are going to use.
There are three types of risk analysis. They are qualitative, semi-quantitative and quantitative. The type of analysis that you do will depend on the data available. In practice, most organisations will generally use qualitative analysis to obtain an indication of risk levels. It is only when more specific and precise indicators are required that quantitative analysis is applied.
Qualitative analysis
Qualitative analysis uses scales to analyse the likelihood of an event occurring and its consequences. These can be used to analyse different risks in different circumstances by simply varying, adapting and adjusting them to suit.
Qualitative analysis would be used in most cases, and is used:
As an initial screening exercise to identify risks that require more detailed analysis
Where the level of risk does not justify the time and effort spent on a more detailed analysis.
Likelihood one
Rating |
Expression |
Attributes |
A |
Extremely likely |
The incident will most probably occur under most circumstances |
B |
Likely |
The incident will probably occur under most circumstances |
C |
Possible |
The incident may occur under certain circumstances |
D |
Unlikely |
The incident is unlikely to occur |
E |
Rare |
The incident will occur under the most exceptional circumstances |
In the same way, consequences arising from an incident occurring may be qualitatively measured.
The following table shows an example of a consequence measure:
Consequences
Rating |
Expression |
Attributes |
1 |
Insignificant |
No injuries, low financial loss |
2 |
Minor |
First Aid Treatment, on-site release contained, medium financial loss |
3 |
Moderate |
Medical treatment required, on-site release contained with outside assistance, high financial loss |
4 |
Major |
Extensive injuries, loss of production capability, off-site release with no detrimental effects, major financial loss |
5 |
Catastrophic |
Toxic off-site release with detrimental effect, huge financial loss |
When the likelihood and consequence are put together, you have an example of the analysis matrix.
Analysis matrix
LIKELIHOOD |
A |
S |
S |
H |
H |
H |
B |
M |
S |
S |
H |
H | |
C |
L |
M |
S |
H |
H | |
D |
L |
L |
M |
S |
H | |
E |
L |
L |
M |
S |
S | |
1 |
2 |
3 |
4 |
5 | ||
CONSEQUENCE |
Legend
L= Low risk, manage by routine procedures
M= Moderate risk, management responsibility must be specified
S= Significant risk, senior management attention needed
H= High risk, immediate action needed
Risk analyses are usually aimed at the negative consequence of risk. The consequence measure therefore reflects the losses and undesired outcome that might arise. However, risk management is increasingly being applied to identify and prioritise opportunities, as the risk associated with not exploiting an opportunity or embarking on a particular business strategy can significant. In many instances, the upside risks are potentially more serious than the risk that negative events will occur, i.e. the downside risk.
When considering the opportunities, the likelihood measure need not change, as it will describe the chance that a benefit will arise. The consequence measure must, however, be adjusted.
An example is as follows: Likelihood two.
Likelihood two
Rating |
Expression |
Attributes |
1 |
Insignificant |
Small benefit, low financial gain |
2 |
Minor |
Minor improvements to image, some financial gain |
3 |
Moderate |
Some enhancements to reputation, high financial gain |
4 |
Major |
Enhanced reputation, major financial gain |
5 |
Outstanding |
Significantly enhance reputation, huge financial gain |
When risks and opportunities are being considered together, a two directional measure of consequence may be appropriate.
Opportunities – two directional process
Negative consequence |
Positive consequence | |||||||||
-H |
-H |
-H |
-S |
-S |
A |
S |
S |
H |
H |
H |
-H |
-H |
-S |
-S |
-M |
B |
M |
S |
S |
H |
H |
-H |
-H |
-S |
-M |
-L |
C |
L |
M |
S |
H |
H |
-H |
-S |
-M |
-L |
-L |
D |
L |
L |
M |
S |
H |
-S |
-S |
-M |
-L |
-L |
E |
L |
L |
M |
S |
S |
-5 |
-4 |
-3 |
-2 |
-1 |
1 |
2 |
3 |
4 |
5 | |
Disastrous |
Significant |
Moderate |
Minor |
Insignificant |
Likelihood |
Insignificant |
Minor |
Moderate |
Major |
Outstanding |
Legend (for opportunities)
L = Low opportunity, manage by routine procedures
M = Moderate opportunity, management responsibility must be specified
S = Significant opportunity, senior management attention needed
H = High opportunity, detailed planning required at senior levels to prepare for and capture opportunity.
Another way in which to measure risk includes the hierarchy of controls. There will be times when you will not have the skills, knowledge and experience to complete a risk assessment of a work area. When this occurs, then you may need to consult with an expert.
Expert advice may include:
Federal, state and local government regulatory authorities
Private consultants appropriate to the risk being evaluated.
When you analyse risk, it is important that you consider costs and the ability of your organisation to implement the control measure you are to put in place. The hierarchy of controls is one way in which control of associated risks can be obtained.
The control measures used to control risk should be chosen according to their effectiveness. The hierarchy of control is a useful tool to use to control risk. The higher up the list you are the more desirable the control measure is. Use the control measures mentioned first to ensure higher control is maintained. There will be times however, when these preferences will not be convenient. When this occurs, you can refer to the hierarchy of controls.
The hierarchy of controls include:
Elimination
Elimination is the most effective method of risk reduction. If you store and handle goods and the dangerous goods or activity is the cause of the risk, then elimination of all risks associated with the dangerous goods will not be likely.
Substitution
You should consider substituting the dangerous chemical with a chemical that does not have such a high risk. When deciding whether or not you will be substituting the dangerous goods with another, make sure that the new substance does not create a different type of risk. You may also need to consider the risks that arise from the storage and handling of the new substance
Isolation/engineering
Isolation of dangerous goods ensures that the risk to people, property and other dangerous goods is controlled by isolation. Isolation is the separation of goods from people and other property including dangerous goods. The physical separation of dangerous goods fulfils two purposes: protecting the occupants from dangerous goods and protecting the dangerous goods from occupants.
Engineering controls are controls which use engineering measures to change the physical characteristics of structures, plant, equipment and processes to reduce the risk associated with storage and handling.
This can be achieved in a number of ways including:
Administrative
Administrative controls are systems of work or safe practices that help to reduce risks associated with the storage and handling of dangerous goods.
Personal Protective Equipment (PPE)
Refer to your organisations policies and procedures on the use of Personal Protective Equipment in the workplace.
The hierarchy of controls however may not be the only controls that you should consider putting in place to control associated risks.
Other control measures that you may use in regards to associated risk include:
Counselling/disciplinary processes
Even though you train your employees to follow policy and procedure, it does not always guarantee that they will automatically follow procedure even if you do explain that they are breaching the law to do so. In some instances, you may not have a choice but to discipline or counsel the employee.
If you are not familiar with these procedures, take the time to learn your organisation’s procedures. Failure to follow your organisation’s procedures correctly may leave you open to litigation.
Housekeeping and storage
If equipment and materials are not maintained or stored correctly, the chance of breakdowns and damage increases. This in turn will decrease your productivity and may expose your team to risks. For example, your sales team have an overhead projector that they borrow from stores and take out regularly to complete presentations to clients.
As the projector is never in the store and is handed from one representative to the next, the projector is never replaced in stores. Control of the projectors usage is maintained through emails. After missing several maintenance checks, the equipment’s electrical lead is damaged. A damaged wire can lead to the risk of electrocution.
WHS records maintenance and analysis
The above example also gives rise to the identification of another problem. By missing regular maintenance, the level of risk will rise. Most organisations will have a maintenance schedule. This schedule will usually vary between states/territories, so make sure that if you travel between states/territories that you are aware of such variances.
These variances will change once the Commonwealth and state/territory WHS authorities negotiate and agree upon a standard act across all states/territories.
Issue resolution
When there is a conflict within a team, attention may stray from safety issues. The moment an issue arises, take steps to resolve the conflict to ensure that staff remains focused on the task of ensuring a safe workplace.
Workplace inspections including plant and equipment
Workplace inspections can be completed internally or externally. External representatives have the right to enter your workplace to complete snap inspections. It is important that your organisation keeps up to date on inspections to ensure that the workplace equipment and plant is safe to use.
Most organisations will have procedures in place for the staff using the equipment and plant to inspect before they use and after they use the equipment. Regular inspections of the equipment and plant should be completed by qualified personnel to ensure that you are providing a safe work environment for your staff.
Activity 3A
3.2 – Include hazard identification at the planning, design and evaluation stages of any change in the workplace to ensure that new hazards are not created by the proposed changes and existing hazards are controlled
Hazard identification
As changes are implemented in the workplace, it is important to be aware of the repercussions of the change. When you introduce any form of change, you need to consider the effect that it will have on the staff that will be impacted by the change. For example, if you change a procedure at one point, it may have a positive impact on that area. However, in the next step of the process, that change may cause problems that will have a negative impact on productivity.
Change is implemented through a support system to inspire your team to embrace the change. One model of change is John Kotter’s model.
The basic steps of this change are summarised as:
1. Increase urgency – inspire people to move, make objectives real and relevant
2. Build the guiding team – get the right people in place with the right emotional commitment, and the right mix of skills and levels
3. Get the vision right – get the team to establish a simple vision and strategy focus on emotional and creative aspects necessary to drive service and efficiency
4. Communicate for buy-in – Involve as many people as possible, communicate the essentials simply, and to appeal and respond to people's needs. De-clutter communications – make technology work for you rather than against
5. Empower actions – Remove obstacles, enable constructive feedback and lots of support from leaders – reward and recognise progress and achievements
6. Create short-term wins – Set aims that are easy to achieve – in bite-size chunks. Manageable numbers of initiatives. Finish current stages before starting new ones
7. Don't let up – Foster and encourage determination and persistence – ongoing change – encourage ongoing progress reporting – highlight achieved and future milestones
8. Make change stick – Reinforce the value of successful change via recruitment, promotion, and new change leaders. Weave change into culture.
If you would like to learn more about Kotter, go to URL Address:
http://www.kotterinternational.com/the-8-step-process-for-leading-change/ (access date: 15/10/2015).
It is important that you also consider the risk involved in planning, designing and evaluating risks.
Potential hazards should be identified, not only by the team, but also by:
Supervisors
Audits, such as independent, external, internal and job safety audits
Workplace processes
Trials of new ideas.
In the planning stage, you must identify any hazards that are present and then design steps to prevent and/or minimise the risk. Risks or hazards are a potential threat to your organisation as failure to identify them will leave you open to litigation for not meeting your duty of care to ensure that the employees work environment is safe.
It is important that you take the time to learn how to perform risk assessments for the state/territory that you reside in. The aim of this section is to provide you with a generic understanding of how to identify, assess and control risks in your workplace.
Common hazards can include:
Hazard |
Potential harm |
Manual tasks |
Overexertion or repetitive movement can cause muscular strain |
Working at height |
Falling objects, falls, slips and trips of people can cause fractures, bruises, lacerations, dislocations, concussion, permanent injuries or death |
Electricity |
Potential ignition source. Exposure to live electrical wires can cause shock, burns or death from electrocution |
Machinery and equipment |
Being hit by moving vehicles, or being caught by moving parts of machinery can cause fractures, bruises, lacerations, dislocations, permanent injuries or death |
Hazardous chemicals |
Chemicals such as acids, hydrocarbons, heavy metals and dusts such as asbestos and silica can cause respiratory illnesses, cancers, and dermatitis |
Extreme temperatures |
Heat can cause burns, heat stroke, and fatigue. Cold can cause hypothermia and frost bite |
Noise |
Exposure to loud noise can cause permanent hearing damage |
Radiation |
Ultra violet, welding arc flashes, micro waves, and lasers can cause burns, cancer, or blindness |
Biological |
Viruses, bacteria, and fungi can cause hepatitis, legionnaires’ disease, Q fever, HIV/AIDS, or allergies |
Psychosocial hazards |
Effects of work-related stress, bullying, violence and work-related fatigue |
When identifying risk, you should make sure that the employee:
Can perform their tasks safely
Is supplied with appropriate tools and equipment, which are well maintained
Does not take unsafe short cuts; and
Ensures that changes that occur have not affected WHS.
Safety is for everyone. Even though you should walk around keeping an eye open for risks, you should also make sure that your team has an awareness of procedures to report and minimise the hazards and resultant risks in the workplace. Review information, records and workers can be utilised to identify ongoing risks.
Information may be obtained from specialists, records can include accident/incident reports and workers who work in an area can assist you in resolving issues by simply identifying possible causes of risk.
Some organisations develop checklists that aim at identifying risk. Once you have identified the risk, you need to assess it.
Assessing risk
Assess associated risk once you have identified the hazards. This is the most demanding step. Risk assessment requires that you estimate the level of risk and then decide the order in which risk needs to be resolved.
When you participate in the risk assessment process, you need to consider the:
Equipment used
The nature of the risk
Number of employees involved in the process
Level of exposure to the risk
Required training
The existing controls.
Likelihood, consequences and the risk analysis matrix (Figures 1-3); and the hierarchy of controls should be utilised here. Let your trainer know if you need to review this process.
One thing that you should note however, is that many states and territories will only use administrative and Personal Protective Clothing (PPE) controls in certain circumstances.
These circumstances include:
When no other control measures will work
For a short term until a more effective way of controlling the risk is achieved
To back up the higher levels of controls.
Activity 3B
3.3 – Develop and maintain procedures for selecting and implementing risk controls according to the hierarchy of control and WHS legislative requirements
Risk controls
The development of controls is considered to exist in the following levels of control:
Choosing the best control measure
Do not introduce the hazard into the workplace. Try to achieve this at the planning stage of a product, process or in the place used. If you design the hazard out in the early stages, you will find that the costs will be lower.
Substitute the hazard
There are times when you must use a certain process to complete a task. For instance, you may be required to use a chemical as part of the processing of a product. There is no way to eliminate the hazard, but you could find another chemical that can perform the same task.
Isolate the risk
This can be done by completely separating the people from the risk. For example, if there are no substitutes for the chemical above and you must use the product as part of the process, then you should consider using remote processes to perform the required process.
Change equipment, workplace and work process
This is not always possible. This always depends on what you are trying to change. For instance if you need to use a chemical as part of a process, engineering controls may only be relevant as far as adding a chemical, however may be relevant as far as whether or not you are going to add equipment to assist in isolating the risk.
Administrative controls
Administrative controls refer to changing procedures. If you have no other chemical that can perform a processing task for instance, and you do not have the funds to isolate the risk or use another product to perform the process, sometimes changing procedures is the only choice you have at controlling the risk.
Use PPE (Personal Protective Clothing)
Using protective clothing is the final resort and can include gloves, protective eye wear, ear plugs and coveralls.
Though it is preferable to choose the higher level of the hierarchy of controls to resolve a problem, there are instances where you have no choice to use a lower level of the hierarchy.
The factors that will influence this decision can include:
Available funds
There are times when the costs of changes will exceed the level of funds available. If a change is too expensive, then the organisation must consider another option.
Availability of the equipment
Is the equipment readily available? Can it be made or be put in place safely?
Its suitability to the workplace
You can recommend a change, but is it appropriate for the workplace. For example, if you recommend a robot to assist in the workplace, you need to consider the size of the equipment, its costs and whether it will fit in the area and whether it is appropriate.
When you make changes to the workplace, to operate effectively you should:
Develop work procedures
Control measures need procedures so that all employees work consistently. Develop the appropriate steps, including safety issues and generate the changes as per your organisations policies and procedures
Provide your team with appropriate training, instruction and information
Close the gap between what the team knows and what they should know. Give support to the team by providing the required level of training, instruction and information. Be clear, honest and safe.
Provide supervision
When workers are inexperienced, a higher level of supervision is required. If not, you may only need to guide them and give them the tools and feedback to perform their tasks competently.
Activit y 3C
3.4 – Identify inadequacies in existing risk controls according to the hierarchy of control and WHS legislative requirements, and promptly provide resources to enable implementation of new measures
Inadequacies in existing risk controls
Once your controls are implemented and employees have been trained to the required level, evaluation should take place to ensure that your control measures:
Are effective
Are safe to follow
Are introduced safely
Are reviewed to ensure that all hazards are identified
Have not been superseded with new work methods, equipment or chemicals to make the process safer
Have been clearly communicated and taught to the workplace in terms of training and instruction
Have been accurately understood so that workers are identifying and minimising risk
Meet legislative requirements and that the severity and health of the workers has not changed beyond minimal risk.
To measure these control areas you can implement the following actions to ensure that they remain effective and include:
Making team members accountable for health and safety – this means making sure that they have the resources required to keep their work area safe
Regular review work procedures and consultation with other team members both internal and external
Effective communication by ensuring that all parties obtain regular feedback through open communication and encourage them
Keeping information up to date including hazard information, risk assessments, training and competency.
Inadequacies in the existing controls should be addressed once the control measures to monitor specific hazards have been identified. An important issue in addressing the hierarchy of controls is the ability of the team to implement recommended changes within the capabilities of the required budget.
Compliance with the hierarchy assumes that there are sufficient resources to implement the safety procedures as required and that any inadequacy should be mapped back to the hierarchy of control.
When inadequacies are identified, review of the organisation’s procedures should be mapped back to the organisation’s hierarchy of control.
Other than the control measures that you put in place, further inadequacies can be identified through:
Internal and external audits
Feedback from team members
Feedback from staff
Innovation
Changes to WHS legislation
The consultative process.
Even if the type of feedback is through unplanned contingencies, you should still consider the impact of the feedback and move to address it if the source of the feedback is credible. Document all changes you make to any of the problems identified. The most feasible change should be implemented and reasons why specific hierarchy controls are missed should be documented.
Activit y 3D
3.5 – Identify requirements for expert WHS advice, and request this advice as required
Seeking expert WHS advice
Changes that are introduced to a WHS cycle are intervention points. It is at these points that your organisation may need assistance to your organisation and those employed there. Different specialists will be able to assist with different interventions. For example, if changes to legislation require staff to be trained, you may require the services of a college or training organisation for employees to obtain the skills they require. In this instance there are two intervention points.
The first intervention point is the change of legislation. The second is the need to change for training. These changes aim to ensure that the workplace remains safe. Without the assistance of experts, incorrect decisions could be made that will have a negative impact on the organisation. Intervention points arise when an action is needed and the employer is unable to facilitate the change.
These changes may require expert WHS advice on:
Advice |
WHS experts |
Testing and analysis |
WHS expert |
Recruitment |
Human resource expert |
Medical and rehabilitation advice Worker cover claims management advice Workplace therapeutic advice Workplace hygiene hazard identification |
Medical practitioner |
Dangerous goods or chemical spill removal |
Supplier |
Financial advice |
Financial expert |
Engineering advice |
Engineer |
Intervention and assistance may be required when:
There is a lack of skill
There is a lack of time
There is a question that needs answering
There are facts that need to be clarified.
When you choose an expert, ask the following questions:
Does the expert have the skills, knowledge and experience to give you the best advice?
Does the expert have the required qualifications?
Are their skills up to date?
Have they done similar work for similar organisations?
Are they members of a professional association?
Specialists can be expensive. Before contacting the specialists make sure that you are prepared. Being prepared will ensure that you do not waste resources and will be able to take action sooner. Collect as much information as you need to provide the specialist with so that they can give informed advice.
Be very clear on what the problem is; its history, background and any incidents that may impact on the hazard. Be clear on the advice that you need. You may even need the implications of the advice and the impact that any recommendations will have on the organisation.
Activity 3E
4. Evaluate and maintain a work area WHS management system
4.1 Develop and provide a WHS induction and training program for all workers in a work area as part of the organisation’s training program
4.2 Use a system for WHS record keeping to allow identification of patterns of occupational injury and disease in the organisation, and to maintain a record of WHS decisions made, including reasons for the decision
4.3 Measure and evaluate the WHSMS in line with the organisation’s quality systems framework
4.4 Develop and implement improvements to the WHSMS to achieve organisational WHS objectives
4.1 – Develop and provide a WHS induction and training program for all workers in a work area as part of the organisation’s training program
WHS induction/training program
All of the goals, objections and actions that your organisation takes must stem from the organisations strategic and tactical goals. For any WHS induction and training program to be effective, the goals of the training program need to match the organisations objectives. To determine the needs of the organisation, a training needs analysis is required. The training needs analysis will ensure that actual training that is needed are completed.
Training needs analysis
When you perform a training needs analysis, you should cover:
The needs of the business – what is the reason for the training?
Gap analysis – what does the organisation want that they do not have now?
Assessment – what are the current skills, knowledge and experience of the people or individual who may participate in the training?
Check point – can the proposed training fill the gap?
Agree to training outcomes – what are the objectives and outcomes required in the training and does the training meet the needs of the organisation?
Delivery methods – what are the appropriate delivery methods to ensure that the team or individual obtains the required skills needed?
Training programs
Training programs may involve:
Enterprise based delivery
This type of training is usually performed in-house by a trainer with the experience to deliver the required training. However, there may be times when the training needed is outside the scope of the experience of employees. This means that the enterprise may need to out-source training.
Provider based delivery
One form of outsourced training includes sending trainees to TAFE or placing the trainee on an apprenticeship/traineeship. These programs can be:
o Fee for service
o Local, state and national curricula
School based delivery
Delivery may need to occur in classrooms. There may be times when the trainee needs more information than you will be able to provide them with. Classroom training gives the trainee an opportunity to participate in group training.
Combination of the above
You may also need to obtain permission from other personnel in your organisation for a member of your staff to participate in training. Consult with the human resource representative before to determine what training is available internally for your staff, including the use of training packages.
Once you have identified the training program(s) that meet your needs, you should also determine the training methods required for your team. The training methods that you can use to reach the workplace goals are:
Demonstration
Trainees can show competence by showing the trainer their new skills. Demonstration can be used during a training session by:
Telling explaining and instructing in what needs to be done
Showing demonstrating the task that needs to be done
Doing the trainees practicing the task that you have shown them
Telling
When demonstrating a task to trainees, you should:
Be clear and concise
Use logical steps
Be brief and keep it simple
Not use jargon
Make sure everyone can hear everything you say.
Showing
When demonstrating a task, make sure that you:
Perform the task at a normal speed to show the trainee the expected standard of service they are to work at
Perform the task at a slow rate, being sure to highlight the main features of the task
Ask trainees to demonstrate the steps involved in performing the task
Offer any assistance that the trainee needs
Give the trainee the opportunity to complete the task on their own.
When you demonstrate the task, ensure that:
All trainees can see the demonstration clearly
You follow a logical order each time you demonstrate the task
You name all equipment and chemicals that you are using
Highlight key points in the demonstration
Invite all trainees to practice and
Give the trainees feedback on their skill levels.
Doing
When demonstrating the task, make sure that the learner has a chance to practice the task as many times as they need to become proficient. Provide the trainee with ongoing feedback on their performance.
When the trainee is completing the task:
Put them at ease if you can
Provide feedback in an encouraging way. Make sure that you highlight the positive areas as well as the areas that need improvement
Ask questions to ensure that the trainee understands what they are doing
Get the trainee to evaluate their own performance
Be prepared to get the trainee to repeat this process as much as they need so they can be comfortable with the training.
Other training methods
Other training methods include:
Discussion and debate
Discussion groups
Lecture presentation
Problem solving and experimentation
Role-playing
Research
Games
Electronic media such as TV, video, and film.
When you choose a training method, make sure that it is appropriate for the learners. For example, if you need to train employees on how to use equipment, research and lectures are inappropriate. Demonstration and observation and even role-playing would be more appropriate as they give the employee the chance to observe you using the equipment, and in turn gives the trainer the opportunity to gain hands on experience in using the equipment.
Activit y 4A
4.2 – Use a system for WHS record keeping to allow identification of patterns of occupational injury and disease in the organisation, and to maintain a record of WHS decisions made, including reasons for the decision
Record keeping
Many organisations use information systems such as databases to identify patterns in their WHS system. For instance, accident/incident reports will identify when an injury or disease becomes common, or if there is a sharp increase in the amount of injuries in an area. This signifies there is obviously a problem with the area that which needs to be addressed.
Other forms of organisational health and safety record keeping may relate to:
Audit and inspection reports to identify faulty equipment
Workplace environmental monitoring records to identify increases in emissions, variances in exposure or changes that impact on the organisations operations
Consultation e.g. Meetings of health & safety committees, work group meeting agendas including WHS items and actions
Induction, instruction and training – identifying whether the training is successful or breaching the gap between present and future desired skills
Manufacturers' and suppliers' information including dangerous goods storage lists – for instance, to establish why there is suddenly an increase in the amount of chemicals used in an area
Hazardous substance registers – to establish what substances are present on the work site
Plant and equipment maintenance and testing reports – is there a decrease in the amount of maintenance on faulty equipment since the organisation updated its procedures?
Workers compensation and rehabilitation records – to establish how much workers’ compensation is costing and what the variances are in the rehabilitation of team members
First aid/medical post records – to establish why there is a sudden increase in minor injuries in the administration office.
Once you identify a variance in the patterns of WHS records, you should implement your organisations procedures to identify the cause of the problem. Identifying the cause of the problem is one of the most important aspects of minimising risk. If you cannot identify the cause of the problem, then you will not have the ability to improve your system.
Once you have defined your problem, then you need to start the WHS process again to ensure the gap that has been identified is corrected.
Activity 4B
4.3 – Measure and evaluate the WHSMS in line with the organisation’s quality systems framework
Reviewing WHS system
To maintain a quality WHS system you need to continuously improve it. Risks will change as the environment changes. For example, you introduce a new piece of equipment to a work site. New risks will arise when the equipment makes a job easier or changes the way in which other tasks are performed. Risk will arise from the introduction of the equipment.
Good WHS management places emphasis on monitoring and reviewing all current organisational plans, strategies, systems and controls. Monitoring ensures that as risks change, new control measures are introduced to control these changes.
Ongoing review of the WHS system is required to ensure that the plan remains relevant to the workplace. Factors that may impact upon risk assessments and control measures can also change over time. This means that the risk management process should be repeated regularly over time to ensure that the risk management process remains effective.
There are many methods that can be used to monitor and review procedures and these should be considered part of your management plan.
You can complete:
Self-assessments
Physical inspections
Checking and monitoring success of actions
Audits and reassessment of risk to achieving objectives; and
Setting of key dates, time frames and deadlines for communicating, monitoring, reporting and reviewing procedures.
Monitor the effectiveness of control measures
When you monitor the effectiveness of control measures, it is helpful to ask the following questions:
Have the chosen control measures been implemented as planned? |
Yes |
No |
Are the chosen control measures in place? Are the measures being used? Are the measures being used correctly? | ||
Are the chosen control measures working? |
Yes |
No |
Have any of the changes made to manage exposure to the assessed risks resulted in what was intended? Has exposure to the assessed risks been eliminated or adequately reduced? | ||
Are there any new problems? |
Yes |
No |
Have the implemented control measures introduced any new problems? Have the implemented control measures resulted in the worsening of any existing problems? | ||
Comments |
This is just one way to monitor as suggested by Australia/NZS 4360:1999 by aligning the objective and values of the organisation to the risk management monitoring and review process.
The risk management system is monitored and evaluated.
You should be able to answer the following questions, which are:
Has the WHS system added value for your company?
Are the outcomes of the program measurable?
Would you make a decision to contract or expand the risk program based on this information?
As a part of the consultative process, it is important that you discuss the hazard with relevant staff members in regards to the review questions.
Consultation
Workers, supervisors and health and safety representatives
What staff should you consult with? Do you have a reporting structure that you need to follow in regards to the site? Does your client have safety representatives that need to be consulted with if you make changes to the way in which a task is performed? If you answered yes to any of these questions, then it is important to consult with them and communicate any changes that you may implement.
Staff members who may be exposed to the control measure
Employees of your organisation may not be the only party that is exposed to risk. Other staff members can include those discussed in the early part of this workplace. However, you may also consider members of the public. If there is any chance that a member of the public is exposed to risk, then it is important to take steps to ensure that they are aware of the risk.
Consult and monitor incidents
Incident reports should be collated and any incidents that arise on a regular basis may be indicative of a problem in the organisation’s processes. You may find it beneficial to follow up and find the cause of the incident.
Review safety committee meetings where possible
Follow up committee meeting to ensure that all problems identified have been followed up and finalised. Committee meetings can also identify the different ways in which a problem could be resolved. If an idea has been considered that is being considered to resolve another problem, then you can find out why the idea was implemented or discarded.
The review process needs to integrate key performance indicators of the organisation. The risk management plan needs to link personal performance and drivers to make sure that they are measurable to the organisation. For example, by changing the way in which a procedure is performed, you will save the organisation money through all of the workers that would have been injured. This ensures that public liability insurance does not increase and occupational health and safety legislation is not breached and fines allocated.
Activity 4 C
4.4 – Develop and implement improvements to the WHSMS to achieve organisational WHS objectives
Improving organisation’s processes
An organisation needs to demonstrate that they are continuously improving their processes, especially if they are registered with the International Standards Organisation (ISO 9000). ISO standards are geared towards helping organisations to meet the needs of their customers and stakeholders with the aim of improving processes. Strict auditing guidelines require that organisation’s continuously improve their processes.
The use of key performance indicators (KPIs) aligned with workplace goals work to ensure that organisation’s processes are improved. Key performance indicators must be quantifiable and agreed upon to reflect the success of the organisation. They are used to provide performance goals to staff.
Quality improvement and KPIs aimed at improving a WHS system should address ways in which:
To improve productivity without putting employees at risk
To define areas in which an organisation needs to improve
To minimise risk
To improve training and the attendance of training
Time lost due to incidents can be reduced and rehabilitation improved.
The size of the organisation and the type of organisation will influence the way in which a WHS system is developed. To achieve the organisation’s WHS objectives, you need to address how to implement the system, its operations and the auditing and review of the process.
WHS system
A WHS system contains five elements including:
1. Policy
Make sure that your system is aimed at WHS improvement and ensuring that your organisation complies with legislative policy.
2. Planning
The effective management of WHS requires that the roles, responsibilities, accountabilities and authority of all staff are defined in the organisations policy and procedures and job descriptions.
These responsibilities may require:
o WHS legal and other obligations
o Hazard identification, risk assessment and control
o WHS Policies aimed at the continuous improvement of WHS processes.
3. Implementation
WHS policies, procedures, objectives, targets, roles and responsibilities should be implemented through rigorous document and data control.
This includes:
Version control
Staff referencing
WHS policies and procedure manuals
Managing hazards
Defining requirements for contractors and suppliers
Developing an appropriate emergency response capability.
4. Measurements and evaluation
Procedures relating to inspection, testing and monitoring including:
Performance measurement
Both internal and external auditing
Incident investigation and external reporting
Records demonstrating compliance.
5. Management review and implementation
Corrective actions used to ensure that the same WHS issue does not arise.
As part of the continuous improvement process and ISO 9000, any inconsistencies and adjustments must be made as they are identified.
Any changes must be processed through the consultative process. Ensure that all staff that will be affected by the change are consulted to ensure that the change or update is necessary and appropriate.
Use the organisations procedures to make sure that you ensure that staff are aware of changes being implemented and advise other levels of management about the change, when it is going to occur, and how.
Activity 4D
4.5 – Ensure compliance with the WHS legislative framework to achieve, as a minimum, WHS legal requirements
Duty of care
Employers have a duty of care to provide a safe work place and systems of work in consultation with their team and to keep their team informed about changes in WHS legislation. To assist you in ensuring that your organisation is compliant with WHS legislation, you can download a copy of the WHS compliance self-assessment from the safety at work process or view the example at the back of this learner guide.
The objective of the WHS Act is to ensure that a safe workplace is created free from risk, illness or injury.
For that end, compliance must be demonstrated in regards to:
A safety management system
Responsibilities and accountabilities
Consultation
Risk management
Information, instructions and training
Managing injuries
Record keeping
Monitoring, review and improvement
Resource management
Corporate risk.
If you are able to work through the document and tick yes the whole way through, then you are complying with current legislation. Care should be taken; this is not a one off process. Instead, as a manager, you are required to ensure that you continuously complying with the legislative system.
Activity 4 E
Skills and Knowledge Activity
Nearly there...
Major Activity – An opportunity to revise the unit
At the end of your Learner Workbook, you will find an activity titled ‘Major Activity’. This is an opportunity to revise the entire unit and allows your trainer to check your knowledge and understanding of what you have covered. It should take between and 1-2 hours to complete and your trainer will let you know whether they wish for you to complete it in your own time or during the sessions. Once this is completed, you will have finished this unit and be ready to move onto the next, well done!
Congratulations!
You have now finished the unit ‘Ensure a safe workplace.’
Appendices
These suggested references are for further reading and do not necessarily represent the contents of this Learner Guide.